Applications P&A
Axing cost with
P&A-on-a-wire
Offshore well abandonments are costly and novel approaches to reducing costs and environmental footprint.
As the industry has greatly changed with respect to performing permanent well abandonments with absolutely no future leaks, due to the potential extreme material and non-materialistic costs involved, it is no longer just the cost of P&A that matters.
We have seen how more and more oil and gas companies are bringing their best people into P&A, as this industry activity is increasingly a focus point for management, shareholders, and the public.
The Axter downhole machining solution enables through-tubing rigless P&A operations with improved P&A results both financially and environmentally.
We like to call the solution P&A-on-a-wire.
Substantial financial upsides
The financial upsides are substantial when moving from traditional rig operations to wireline-conveyed light intervention vessel operations. This potentially reduces operating costs by up to 80 %. Wireline-conveyed light intervention vessel operations also enable operators to reduce their balance sheet for future commitments by utilizing rigless technology.
Axter allows controlled cutting and optional removal of annular control lines and cables. This approach enables cost savings of up to 80% and emission reductions of up to 90%.
Reducing emissions
Moving subsea P&A operations from rig-based to rigless offers substantial emission reductions. Consequently, our complex, flexible and powerful wireline wellbore intervention tool, the Axter, has now been launched.
The tool was initially developed for rigless operations, enabling permanent isolation of tubing strings with control lines/cables (microtubes) downhole.
More metal in the ground
The tool will locate the microtube(s), mill a window in the tubing adjacent to the microtube and extend a gripper to secure the microtube, followed by controlled cutting of this through the window created.
This allows shallower cutting of the tubing to leave as much “metal” in the ground as possible, while still enabling placement of a suitable abandonment isolation barrier. More “metal” in the ground reduces the need for tubing handling, transport and discharge, leading to less emissions.
Improving safety and sustainability
By moving from rig to vessel-based operations and leaving more of the well completion in the hole, there are large and tangible GHG savings. This is based upon typical rig-based operations (and timings associated with conventional P&A and full tubular recovery) of approximately 60,000 kilos CO2 used per day.
In addition, the risk to human life and potential environmental impact is reduced by minimizing hazardous handling operations & radioactive disposal.
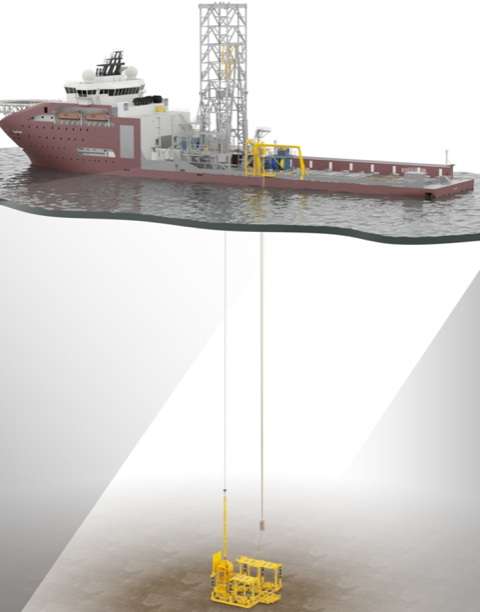
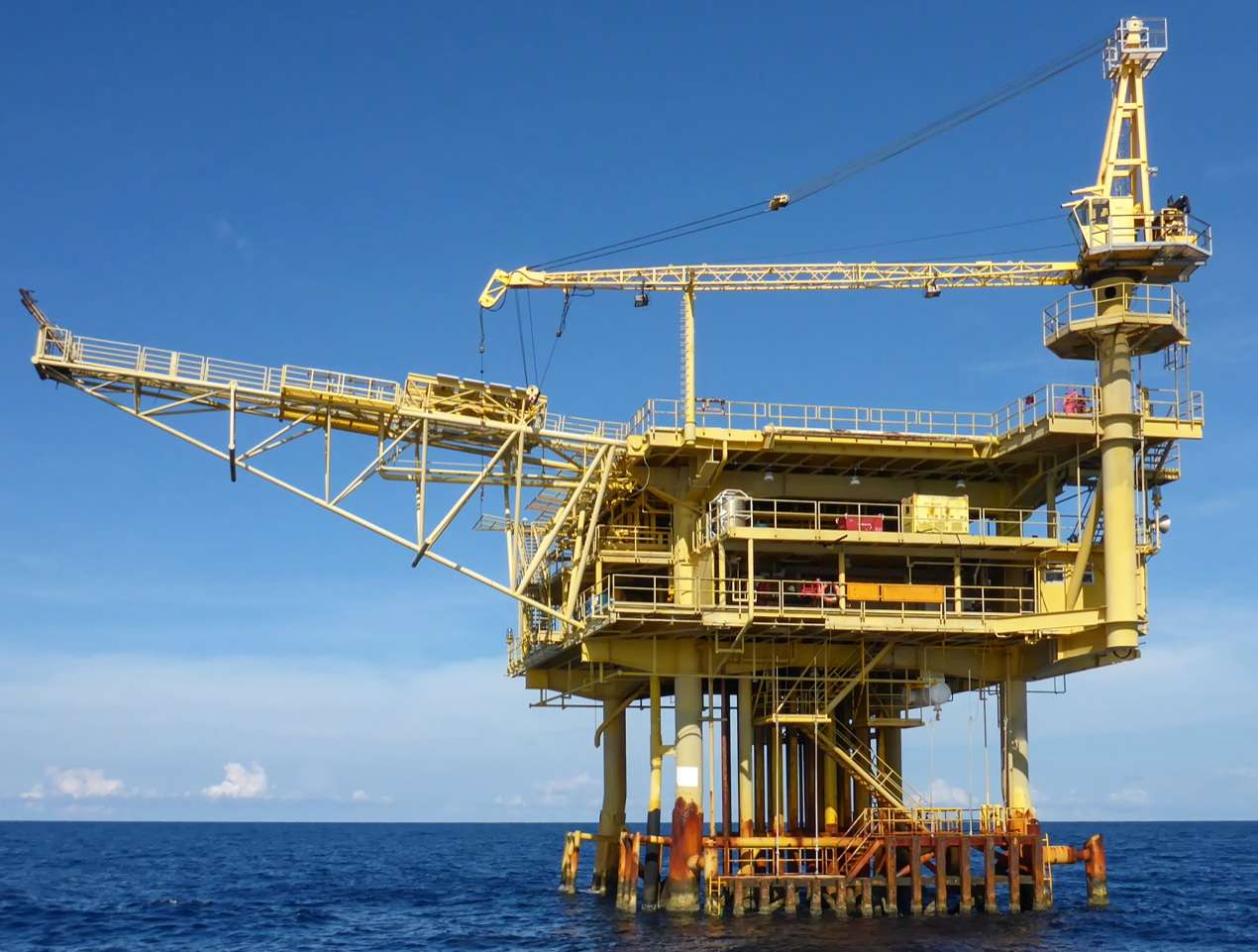
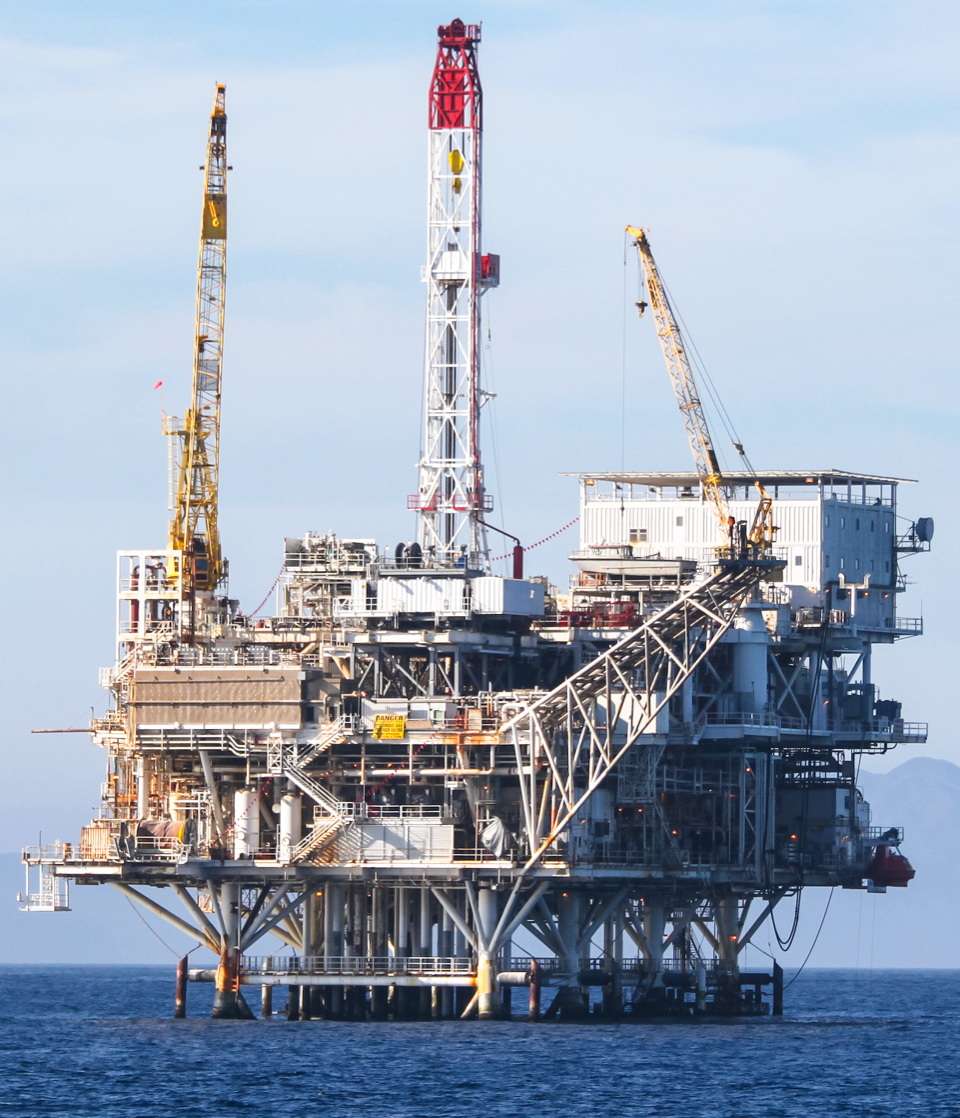